Technology In Shipping: Improvements in Vessel Efficiency
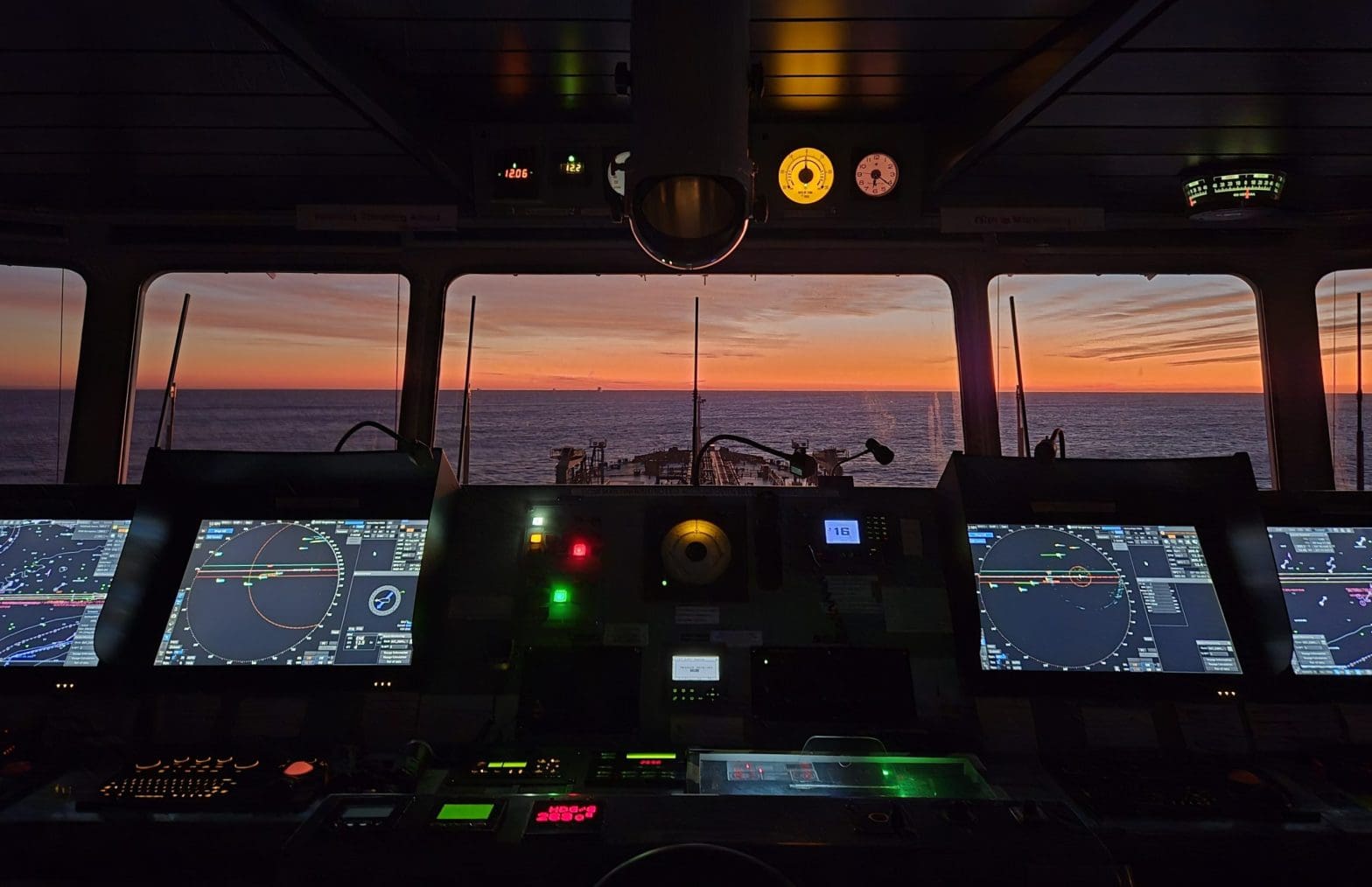
For the marine sector, innovation led change is nothing new. Consider the impact that radar and satellite communications have had in the past one hundred years alone. But the industry now faces a tipping point, where technological developments such as autonomous and smart ships are turning the realms of science fiction into fact. At the same time, the sector is facing unprecedented cost pressures and a stricter regulatory backdrop, as environmental restrictions persist and harden.
In the current scenario, a wide range of options exists to improve vessel efficiency, reduce fuel consumption and lower emissions. They might be categorized into a few broad categories:
- Hull form optimization: Issues related to the basic hull form design including selecting proper proportions, reducing resistance by optimizing the hull form and appendage design, and assessing the impact on the resistance of waves and wind.
- Energy saving devices: These are devices used to correct or improve the efficiency of propellers as well as developing technologies aimed at reducing the hull frictional resistance or using renewable energy sources (such as solar and wind energy).
- Structural optimization and lightweight construction: These concepts relate to the impact of the use of high strength steel on lightship weight and energy consumption.
- Machinery technology: Advancements in this area concentrate on the efficiency gains that are possible in the design and operation of the ship’s machinery and systems. It covers main and auxiliary diesel engines, waste heat recovery and other auxiliary equipment.
- The fuel efficiency of ships in service: This category addresses operational measures that can reduce fuel consumption. These include voyage performance management, hull and propeller condition management, optimum ship systems operation and overall energy efficiency management.
It is evident from the above that categories 1 and 3 address challenges for new vessel construction, whereas the remaining categories (2, 4 and 5) cover both newbuilds and existing vessels.
1. Hull form optimization:
Parameters that are to be optimized are ship size (capacity), service speed and principal dimensions. In order to minimize hull resistance and increasing propulsion efficiency, the following may be carried out:
- Optimize the forebody: Use of bulbous bows for optimizing the forebody shape.
Refer Fig 1: Bulbous bow: The green line characterizes the ordinary bow wave of the hull. The blue line characterizes the wave formed by the bulb. The red line is the sum of these two. The altitude of the bow wave is noticeably reduced, which reduces the hull drag associated with the bow wave. This improves fuel economy and increases range.
- Optimize aft body: Efforts to reduce stern waves/improve flow to propeller/avoid eddy effects
- Appendage resistance: Twin ‘skeg’ design
- Manoeuvring and course keeping considerations: Performance predicted through model testing in a towing tank, etc.
- Hull coatings: These can lower frictional resistance and limit fouling by aquatic organisms. A saving between 1-9% fuel consumption can be achieved if a proper hull coating has been carried out.
2. Energy-saving devices:
Different devices have been used to optimize the energy performance of ship designs. Also, recent developments have led to a series of devices aimed at reducing the hull frictional resistance/ exploiting readily available natural resources, such as solar or wind energy:
a) Propulsion improving devices (PIDs):
- Wake equalizing devices: These improve the flow around the hull like Grothues Spoilers, wake equalizing ducts, stern tunnels, etc.
- Pre-swirl devices: This condition the wake flow and improve the angle of attack towards the propeller blades, eg. Mewis ducts
- Post-swirl devices: These reduce the detrimental flow characteristics around the propeller and increase rudder efficiency, eg. rudder bulbs, propeller boss caps, etc.
- High efficiency propellers like controllable pitch propellers (CPP), ducted propellers, Kappel propellers (modified blade tips), etc.
b) Skin friction reduction:
Viscous resistance accounts for the great majority of the hull resistance in the water. To reduce the same, various techniques are being tried out to varying levels of success:
- Air cavity systems: A thin layer of air is formed and maintained over the hull flat bottom
- Micro-bubbles: Micro-bubbles created around the hull surface to reduce resistance (in trial stage)
c) Renewable energy:
Wind and solar power are also being considered, especially in the generation of auxiliary power:
- Wind energy: Rotor sails, Flettner rotors are being developed. These utilize a so-called “Magnus Effect” for generating energy.
- Solar: Solar panels have been used on some vessels (eg. the NYK car carrier Auriga Leader) which is equipped with more than 300 such panels. High capital expenditure is an obvious drawback in this area.
3. Structural optimization and lightweight construction:
Structural weight reductions have a great effect on the required power for faster and smaller vessels like fast ferries. Structural weight optimization for large cargo vessels (displacement hulls) increases the available deadweight for a ship of the same size, thereby improving transport efficiency.
4. Machinery technology:
Proper consideration of available technologies to improve the energy efficiency of main and auxiliary engines must be framed by the primary energy source – fuel.
a) Prime movers – Main and auxiliary engines:
- Diesel engine energy efficiency enhancements: Electronic control engines, use of Alpha lubricators, Exhaust gas bypass systems, Variable turbocharger area (VTA), engine de-rating, etc.
- Main engine efficiency measurement instrumentation: The use of shaft power meters, mass flowmeters for fuel, etc.
- Main engine performance measurement and control: Use of computer-based systems for monitoring cylinder and fuel injection system performance are widely used, such as PMI On-line.
b) Auxiliary equipment:
- Variable speed motors: These improve the operating efficiency of pumps and fans that operate at variable loads. This technology is especially beneficial for equipment that operates at variable loads.
5. The Fuel efficiency of ships in service:
The most direct and useful tools for improving a vessel’s performance are the operational decisions made daily on how to conduct a voyage, perform regular maintenance and monitor fuel consumption efficiencies. Accurate and regular energy use monitoring across the fleet can highlight inefficiencies and provide a mechanism for continual improvement.
a) Ship operation: Voyage performance management:
- Voyage speed optimization: This has a dramatic impact on fuel consumption because the speed is related to the propulsive power required by approximately a third or fourth power relationship.
- Weather routing – safe and energy efficient route selection: It selects a course from the departure port to the destination port that provides the safest passage and reliable on-time arrival while considering actual wind, wave and current conditions expected during the voyage.
b) Hull and propeller condition management:
Taking care of the propeller and underwater portions of the hull is all about minimizing roughness. Regular in-service cleaning to remove fouling organisms (which are a form of roughness) is beneficial unless it is carried out in a way that results in a damaged coating or one that has been ‘roughed’ up. Within the domain of our company, available technology is utilized to enhance energy efficiency:
Hull form optimization
Our company vessels have been constructed with an optimized hull form most suited to the expected operating profile during service:
- Usage of a bulbous bow to reduce the wave- making resistance
- Effective external hull coatings
- Larger rudders provided resulting in increased course-keeping effectiveness
Energy-saving devices
Many of our vessels are provided with the following energy-saving devices:
- Becker-Mewis ducts
Machinery technology
Our fleet vessels have been built to “Eco-design” with the following carefully borne in mind:
- Electronic controlled engines
- Alpha lubricators
- Exhaust gas bypass systems
- Mass flowmeters
- Engine auto-tuning, PMI online
- Use of variable speed motors
The fuel efficiency of ships in service
- Leverage the potential of data for evaluation of vessel performance
- Regular in-service hull cleaning
Increasing ship efficiency is a combination of multiple factors, which plays an important role. With lofty targets in place, there has been a consistent rise in the incentives and regulations for improving ship energy efficiency.
There is considerable potential for reducing emissions in the shipping sector. A lot of the technologies are already available, and some are relatively easy to implement: slow streaming, improved voyage planning, trim optimization, hull coating and propeller cleaning. There are also a plethora of technologies available for retrofitting on existing vessels; main engine tuning, propeller and rudder upgrades, fin and duct energy-saving devices, to name a few. Not all solutions can be applied to all types of ships, and individual saving measures cannot simply be added together. The current uptake of many of these technologies is limited due to the cost of implementing them and a lack of knowledge regarding their effectiveness on specific ship types/sizes/routes.
What are your thoughts about the various practices for increasing ship efficiency? Any insights on how you ensure increased efficiency in your own way?
References:
- Study on energy efficiency technologies for ships // CLIMA.B3/ETU/0023r // European Commission
- L. Larsson et. al., 2010, “The Principles of Naval Architecture Series: Ship Resistance and Flow,”
- Specialist committee on energy saving methods – Proceedings at the 28th International Towing Tank Conference (ITTC) 2017
- ABS Ship energy efficiency measures – Status and guidance